Chile Pioneers Region’s First 3D Printed ‘Seed House’
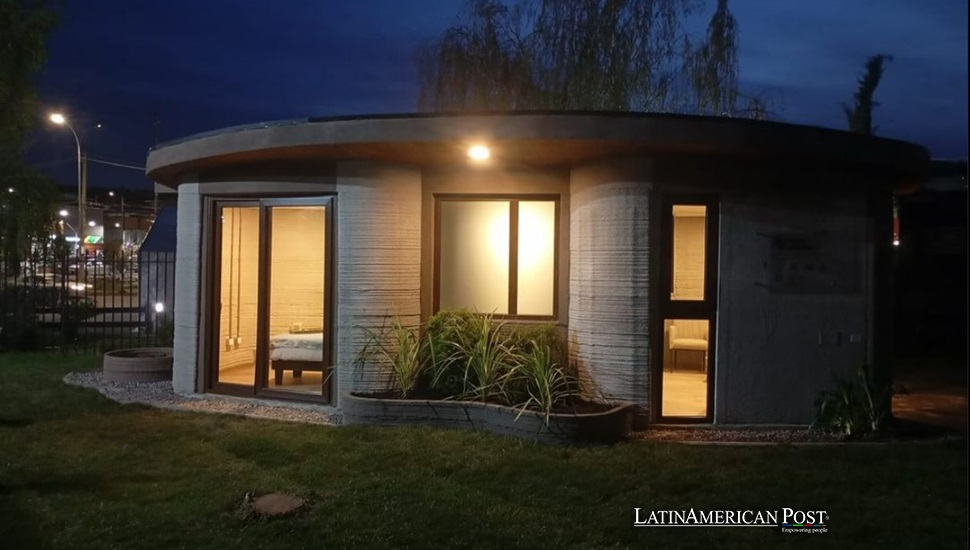
In a groundbreaking project, a university team in Chile has created Latin America’s first 3D-printed concrete home. This innovative construction technique could revolutionize the building industry in a region with high housing demands and unique environmental challenges.
A Revolutionary Step in Construction
In a significant advancement for the construction industry, a team from the University of Biobío in Chile has built Latin America’s first 3D-printed concrete house. The “seed house,” or Casa Semilla, is a compact, efficient structure created using cutting-edge 3D printing technology. Utilizing an Atenea-UBB printer and a KUKA KR120 industrial robot, the team developed a method for printing concrete walls layer by layer, controlled entirely by a computer system. This process represents a bold shift away from traditional building methods, potentially heralding a new era for the construction industry.
The project was completed in 29 hours, with the team assembling the finished house over two days. The walls, made of printed concrete, were manufactured at the university’s laboratory, marking a significant technological achievement for Chile. Claudia Muñoz, an academic at the university’s Faculty of Architecture, emphasized the efficiency of the process. “We print these industrialized walls entirely in our lab,” Muñoz told Reuters.
The Casa Semilla covers an area of approximately 30 square meters and comprises seven walls made entirely from 3D-printed concrete. As the first of its kind in the region, the house showcases the potential for rapid, cost-effective, and innovative building solutions in Latin America.
The Potential to Change Construction
Rodrigo García, a vital member of the university’s Manufacturing in Construction Group, explained to Reuters that the project could reshape how construction is approached in the region. The 3D printing method introduces a flexible building model that could reduce time and cost in an industry often characterized by inefficiency and lengthy processes.
“This is a very revolutionary technology because it changes the traditional way of building, where plans are made, products are quoted, a large number of elements have to be purchased, and the land prepared, which is time-consuming,” García said. 3D printing in construction allows for a more streamlined process, with minimal material waste and precise execution.
However, García acknowledged that there are still questions regarding the technology’s cost and reliability. Although promising, the method requires further testing to determine its scalability and effectiveness for larger projects or in varying environmental conditions. This new technology could revolutionize the construction sector, particularly in regions facing housing shortages and budget constraints.
The house was erected on land owned by a private construction company in the Torreones neighborhood of Concepción. The company’s involvement in the project suggests a growing interest from the private sector in exploring innovative construction technologies.
A Solution for Latin America’s Housing Demands?
The potential for 3D-printed homes to address Latin America’s significant housing demands is particularly intriguing. As the region struggles to meet the needs of its growing population, innovative approaches like this could offer a solution. The ability to build homes quickly, with minimal waste and at a lower cost could transform housing markets in countries facing severe shortages.
García believes this technology could be part of a broader shift in how construction is viewed in Latin America, where traditional methods are often slow and expensive. “We have many housing demands in Latin America, and we are used to importing things,” García told Reuters. “This is a complex change to adopt, which has to be adapted to our Chilean reality rooted in earthquakes and our variety of climates.”
Latin America’s unique environmental challenges, such as frequent earthquakes in countries like Chile, present additional hurdles for the widespread adoption of 3D printing in construction. The technology must be adapted to ensure that buildings can withstand natural disasters and varying weather conditions. Nevertheless, the successful construction of the Casa Semilla suggests that such adaptations are possible.
Future Prospects for 3D Printing in Construction
The successful development of Chile’s 3D-printed seed house marks the beginning of what could be a transformative period for construction in Latin America. As more private companies and governments recognize the potential benefits, investment in this technology could increase, leading to further innovations and improvements in the construction process.
While there are still questions to be answered, such as the long-term durability of 3D-printed homes and their ability to scale for mass production, the potential is undeniable. The ability to rapidly build homes with precision and minimal waste could prove invaluable in a region where affordable housing is often in short supply.
For now, the team behind Casa Semilla is focused on refining its technology and ensuring that it meets the specific needs of Chile and other Latin American countries. As García told Reuters, “This is not just about technology; it’s about changing mindsets and adapting new methods to fit local realities.”
Also read: Mexico’s Cybercrime Crisis: Over Half of Latin American Attacks Target the Country
With the successful construction of Latin America’s first 3D-printed home, the construction industry’s future looks more innovative than ever. The Casa Semilla represents a significant milestone for Chile and the entire region as it explores new ways to meet housing demands in the face of environmental and economic challenges.